Automation Isn't Just for the Shop Floor
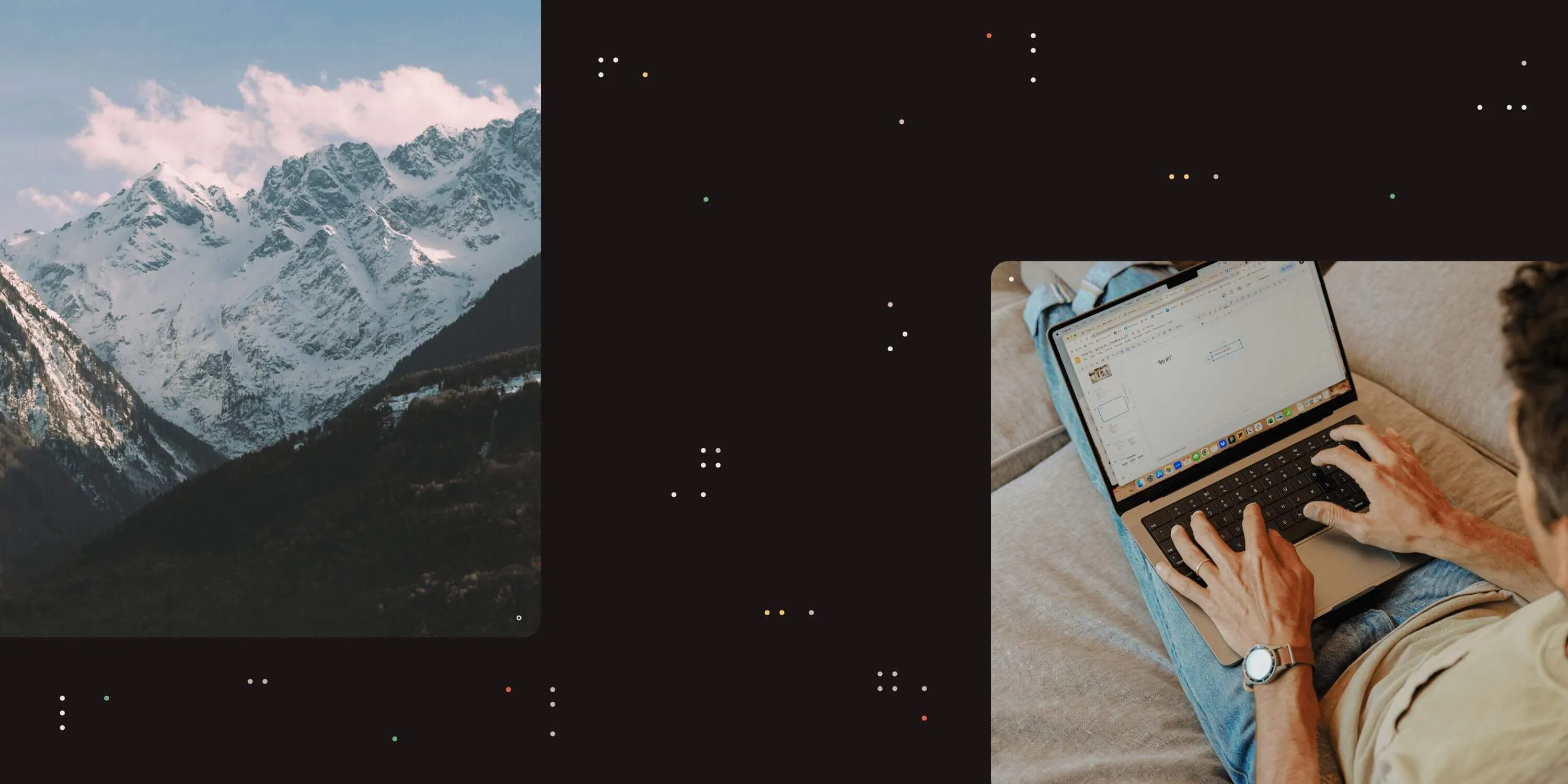
Picture an autonomous mobile robot (AMR) moving through a factory. Quietly and efficiently, it moves materials, components, subassemblies, and finished products between warehouses, production lines, packaging, and shipping. There’s no human involvement, no accidents, and no mistakes; the movement happens dependably and predictably.
Why can’t administrative processes happen the same way? Well, the simple answer is that they can. For a long time, manufacturers have focused on automating what happens on the shop floor. They’ve sought to eliminate manual labor, and this effort has yielded immense benefits. Now it’s time to apply the same thinking to office workflows.
Manufacturing Productivity and Efficiency
Recent years have seen many factories become highly automated. Not only do the machines themselves run without human involvement but so too do the handling systems. These deliver products, load and unload, and take processed material or items to the next step in the process.
In high-volume manufacturing – consumer goods and automotive production spring to mind – conveyors of various types have provided the movement. Robots take the strain when parts need loading and unloading from machines, saving people from the heavy lifting. Today manufacturers are starting to deploy AMRs that move material, components, and even tools to where they are needed.
Factory automation is known for removing people from dull, dirty, and dangerous work, but there’s another, often overlooked, benefit: automation increases consistency. When a task is automated, it’s performed exactly the same way every time. Human workers can’t manage that, no matter how hard they try.
An inspection provides a good example. Tired and distracted human inspectors miss defects that should be caught before they reach the customer. At the same time, as humans are inherently subjective, a good product is sometimes scrapped unnecessarily. By being repeatable and consistent, automated inspection solves these problems.
Human variability is a problem when processes are supposed to be standardized. It leads to omissions and errors, and tasks can take longer than they should. That disrupts downstream operations and hits productivity and efficiency. Conversely, once automated, they are repeatable, consistent, and reliable.
Key Elements of Factory Automation
Industrial manufacturing is currently going through a fourth revolution. The history looks like this:
- Steam power takes over from human and animal energy sources – the First Industrial Revolution
- The Second Industrial Revolution involved a switch to electricity, oil, and gas, accompanied by the development of the telephone and telegraph.
- Computers and PLCs brought about the Third Industrial Revolution and gave us the automation seen today in most factories.
- Inexpensive sensors, coupled with internet communication, advanced analytics, and even AI, are bringing about a digital transformation, a Fourth Industrial Revolution sometimes referred to as “Industry 4.0.”
As we see it in factories today, automation is characterized primarily by PLCs and computers running programs that control motions and actions. Motors power slideways, spindles, and conveyors, with encoders reporting speed and position. Solenoids open and close valves and gates in response to signals from the controllers while sensors report back so that processes can continue.
The digital transformation will reduce waste while increasing utilization measures like OEE and boosting efficiency. Breakdowns will go away as machines become able to report their condition to a maintenance system that schedules overhauls and repairs. Quality will rise as machines adapt to changing conditions, environmental or material-related, and people will move from repetitive tasks to more creative, forward-thinking, problem-solving roles.
Office Workflows and Automation
Factory automation is essentially about moving data now and increasingly in the future. The same is true of the processes used to run every business. In some cases, these are codified as procedures (usually when required for the Quality Management System (QMS)); in others, there are informal or loosely defined ways of doing things.
Examples of well-defined work processes (in most organizations) include:
- Paying bills
- Documenting training
- Calibrating measurement devices
Processes that lack well-planned and implemented procedures might include:
- Near-miss reporting
- Supplier selection
- Monitoring indirect material consumption
These, and the many others that exist, are characterized by paper forms, folders, spreadsheets, and the occasional template. For each, the workflow involves people creating or initiating documents, adding information, and passing them along to other people. In many cases, most requests, for example, need feedback from the originator that tells them what to do next. Many also need storage to provide an audit trail or a (somewhat) searchable history. In manufacturing terms, office and administrative tasks automation is somewhere between the second and third revolutions.
What is Workflow Automation?
For certification to a Quality Management Standard like ISO 9001, how tasks are done is documented as a series of steps. This is the workflow. Most organizations use descriptive documentation, but flow charts work just as well. (Some will argue they are less ambiguous and, therefore better.)
Workflow automation refers to using software that implements those flow charts. It doesn’t take away human involvement or decision-making but automates data movement. In a sense, it’s analogous to a factory conveyor or AMR: it moves the data from one step in a process to the next. Moreover, because it prevents shortcuts and non-standard ways of doing things, it could even be thought of as a poka-yoke for paperwork!
Taking the analogy further, in an automated workflow, the software notifies the “machine” that a new job or batch has arrived and is awaiting processing. This is like having sensors on a conveyor. We could even imagine monitoring the queue length and raising a flag if it becomes too long.
As is quality control, storage and analytics are integral to an automated workflow. Metrics are readily implemented. Errors and omissions are detected immediately they occur, or better still, prevented by poka-yoke type “mechanisms”.
Examples of Workflows That Can be Automated
Any sequence of tasks that needs performing regularly is a candidate. Examples can be seen in:
- Document approval processes
- Safety reporting
- Raising purchase orders
- Travel expense approval
- Product lifecycle development
The Benefits of Workflow Automation
Automating workflows in office and administrative processes yields very similar results to automating manufacturing processes. They include:
- Higher quality – in an automated workflow process, the software can check for errors and notify those responsible immediately. Not passing incomplete or incorrect data through the system saves a lot of time and improves record accuracy. Workflow management also stops people from taking shortcuts and prevents promises of “following up with the paperwork later.”
- Less manual work – completing the repetitive, predictable activities integral to so many office processes saves time, freeing up people for more productive work.
- Faster processing – automation reduces the variable delays that clog bottlenecks and slow progress everywhere to a crawl.
- Quicker new product development – documentation and approvals often cause delays while working on the next generation. By accelerating processing, automation helps get new products to market faster.
- Lower costs – as with manufacturing automation, faster processing, higher accuracy, and less need for human input- lead to lower costs.
Process Automation in the Office
In manufacturing, using automation to cut costs, lead time, and improve quality has long been a way of life. It’s past time that the same thinking was applied to workflows in the office. Today it’s both feasible and practical to save time and money by automating many office processes.
Nutrient Workflow helps companies work more efficiently by automating repetitive, high-volume workflows. This improves quality, accuracy, and consistency, ensures adherence to the defined procedures, saves people from dull, repetitive tasks, and speeds up information flows. Contact us to learn more.