Lean principles for workplace efficiency
Table of contents
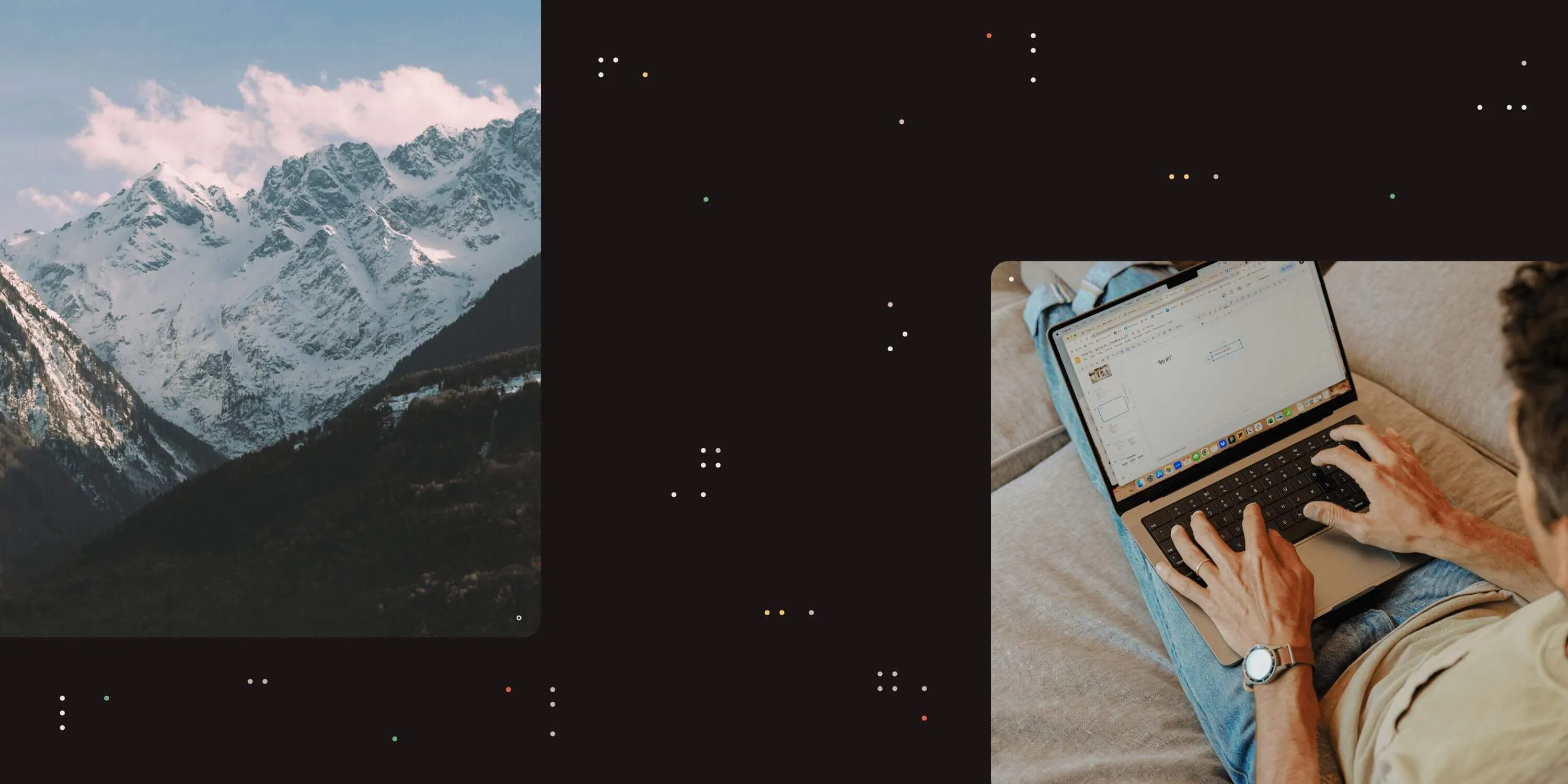
Regardless of how efficient and productive you may already be, there is always room for improvement. By embracing lean principles, including defining value, mapping the value stream, creating flow, and pursuing perfection, you will become more effective, efficient, and productive.
Lean thinking(opens in a new tab) is a strategic management framework (based on principles practiced at Toyota) with origins in manufacturing and production—where it's one of the most popular approaches to work. For example, according to research outlined in a 2021 Manufacturing Digital article(opens in a new tab), nearly 70 percent of manufacturers use lean practices—often with incredible results (according to another study(opens in a new tab), lean manufacturing increases productivity by an impressive 35 percent).
But lean principles aren't exclusive to optimizing the manufacturing and product creation process; you can apply some of the core lean principles (including defining value, mapping the value stream, creating flow, and pursuing perfection) to increase workplace efficiency and boost productivity across the board—no matter what the industry or end product.
But the question is how can you apply lean principles to your workflows (both organizational and individual)—and become more effective, efficient, and productive in the process?
Let's take a look at a few fundamental principles of lean thinking and how to apply them to increase workplace efficiency and boost productivity:
Define Value
The goal of lean thinking is to achieve success as efficiently as possible. But you can't achieve success if you don't know what success means—which is why defining value (and, more specifically, how your customers represent value) is the first principle in the lean framework.
Understanding what your customers want, need, and value is crucial; it lays the foundation for creating products and services (as well as processes and workflows) that deliver on those wants, needs, and values most efficiently—and ensures that the work you're doing is ultimately going to land with your customers.
How to apply the principle to increase workplace efficiency and boost productivity
Before you move forward with anything work-related, make sure to get clear on the end user's definition of value—for example, by conducting one-on-one interviews, surveys, or market research. Also important to note? Depending on what you're working on, the end users may be your customers—but they may also be internal stakeholders (for example, if you're developing a process to track your team's work hours more efficiently).
Map the Value Stream
The following lean principle is mapping the value stream. Think of the value stream as a road map; it outlines every step, system, and process you use to get from the beginning to the end of your workflow. For example, let's say you're using lean principles to develop a new software. In that case, your value map would include all the steps and processes your organization needs to move forward with to develop, create, and sell that software—from competitor research to developing the code to QA testing to design and marketing.
Once you have everything mapped out, you can identify inefficiencies (aka "waste")—and eliminate them to make your operations streamlined and more efficient. For example, upon mapping the value stream for your product, you might realize that the ticketing system your engineering team is using is creating bottlenecks and slowing down the code approval process—in which case you might research alternatives to streamline your tickets, "eliminating waste" and increasing overall efficiency.
Applying the principle to increase workplace efficiency and boost productivity
Mapping the value stream is an effective strategy for improving efficiency and boosting productivity at the organizational level (like the above example). But you can apply this principle to identify inefficiencies in any process—including individual workflows.
Map out your daily workflow and look for ways to eliminate waste and increase efficiency. For example, is email taking up hours of your day? Invest in an email management tool that organizes your inbox and prioritizes your most important messaging—and take some of that time back to focus on the work that matters. Or maybe you're working on a project—but you have an hour every day waiting for your boss' approval on your deliverables before you move forward. In that case, you might brainstorm faster, more efficient ways to get your work approved with your boss—so you're not spending an hour waiting on approval when you could be moving the project forward.
Create Flow
Once you've eliminated waste, you should be left with the steps that create real value. And that's when it's time to apply the next principle of lean thinking—creating flow.
Creating flow is about optimizing things so that there's little-to-no friction between steps—ensuring that your output "flows" to the end user as smoothly as possible. Depending on the situation, this might mean implementing technology or software to connect disjointed steps in your processes—or it could mean coordinating with other teams or co-workers to create more flow between teams, departments, and/or employees.
How to apply the principle to increase workplace efficiency and boost productivity
You've already eliminated unnecessarily wasteful steps; now, it's time to look at your remaining steps and figure out how to optimize them in a way that things run (or "flow") as smoothly as possible. For example, let's say you're an engineer working on launching a new software. To create flow, you might coordinate with your market research team to develop a system that allows for seamless communication of market testing feedback and engineering changes—so that customer feedback is getting to engineers, engineers are making changes to the product, and market testers are then testing those changes in the most streamlined, effective way possible.
Pursue Perfection
Lean thinking isn't a "one-and-done" framework. If you want to continually increase workplace efficiency and boost productivity, you must constantly examine—and optimize—your processes and approach.
In other words, you need to be pursuing perfection.
As the title suggests, the last principle of lean thinking, pursuing perfection, is about continually striving for excellence. It's about recognizing that, no matter how efficient and productive you are (as an individual, team, or organization), there is always room for improvement—and if you want to be your most efficient, you need to be looking for that room for improvement and acting on it on an ongoing basis.
Applying the principle to increase workplace efficiency and boost productivity
Review your systems, processes, tasks, and projects regularly. Apply all the principles of lean thinking to continue to identify improvement areas—and move towards increased efficiency and productivity.
For example, let's say you just launched a software. You might review the launch every 30 days to identify potential areas where you can increase efficiency; that way, you're continually evaluating the software and launch plan and making adjustments as necessary.